Irkut MC-21/PD-14
The project is to use SIAL-type material in the nacelle of PD-14 engines designed for Irkut MC-21 short- and medium-haul aircraft.
⚡️ Introduction
The PD-14 engine (Fig. 1) is designed for Irkut MC-21 short- and medium-haul aircraft (Fig. 2), as well as for industrial gas pumping units. The main purpose of its creation is the development of a modern and efficient gas generator with an increased degree of technical perfection and with characteristics allowing it to create a family of engines of various capacities on its basis.
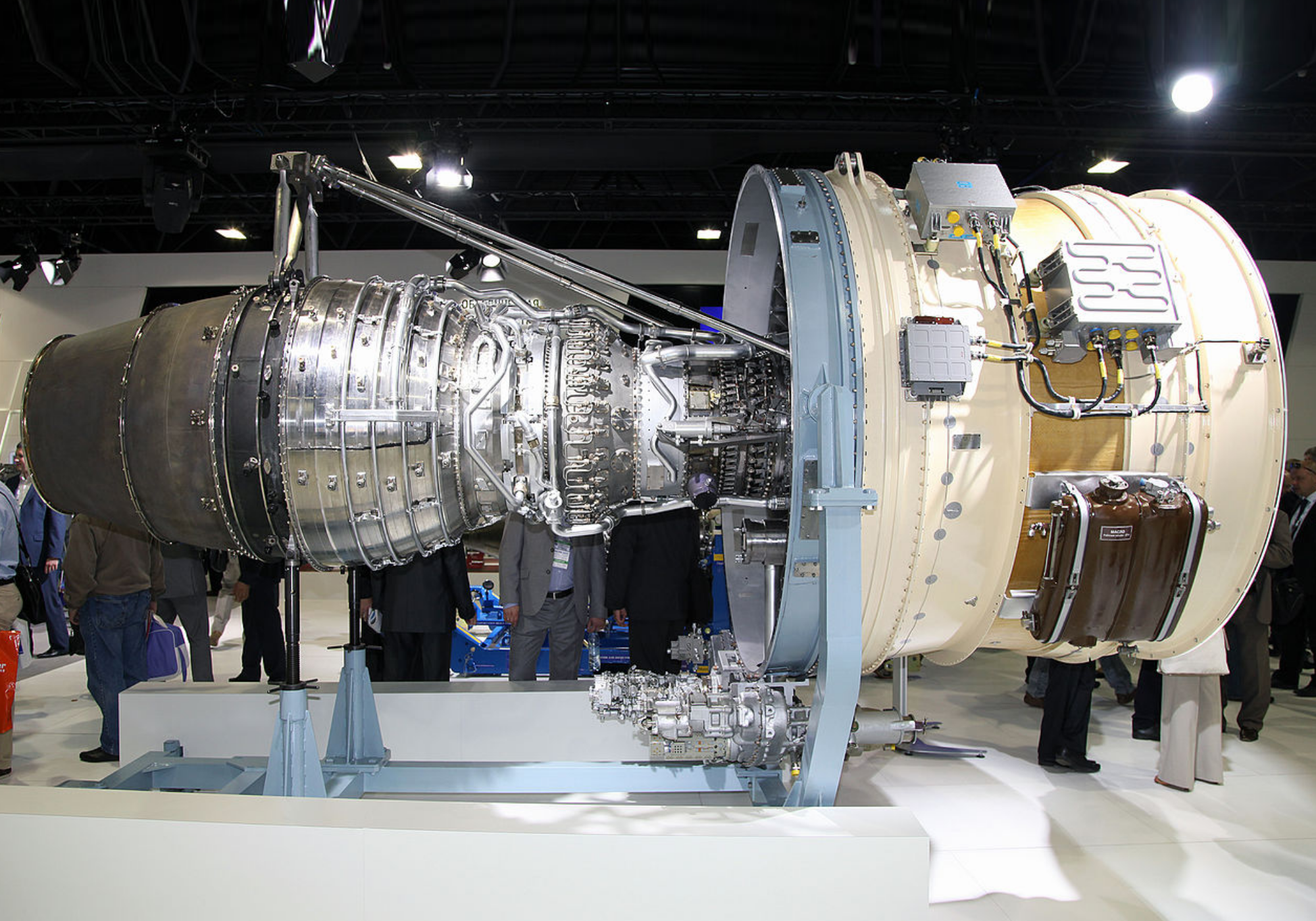
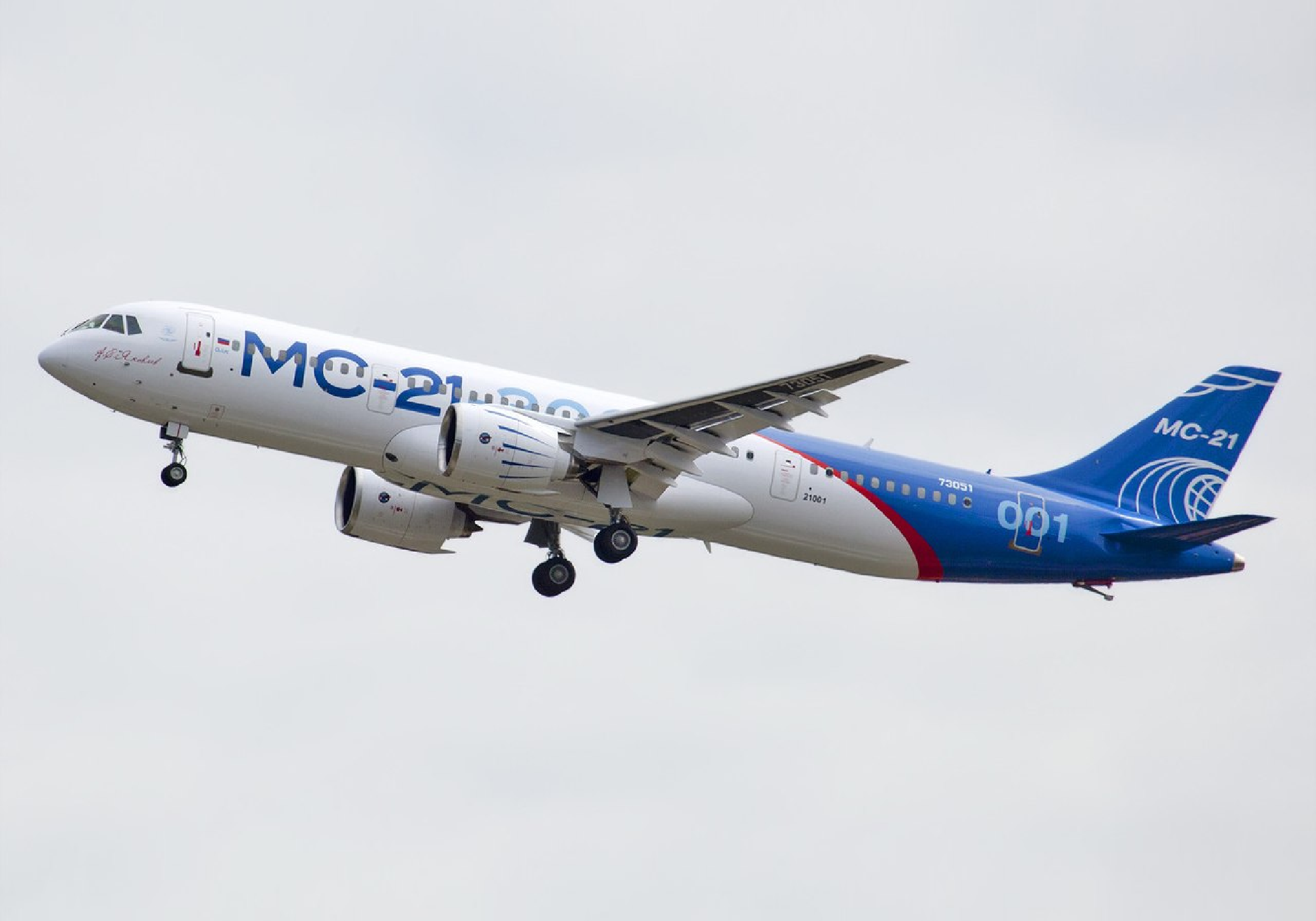
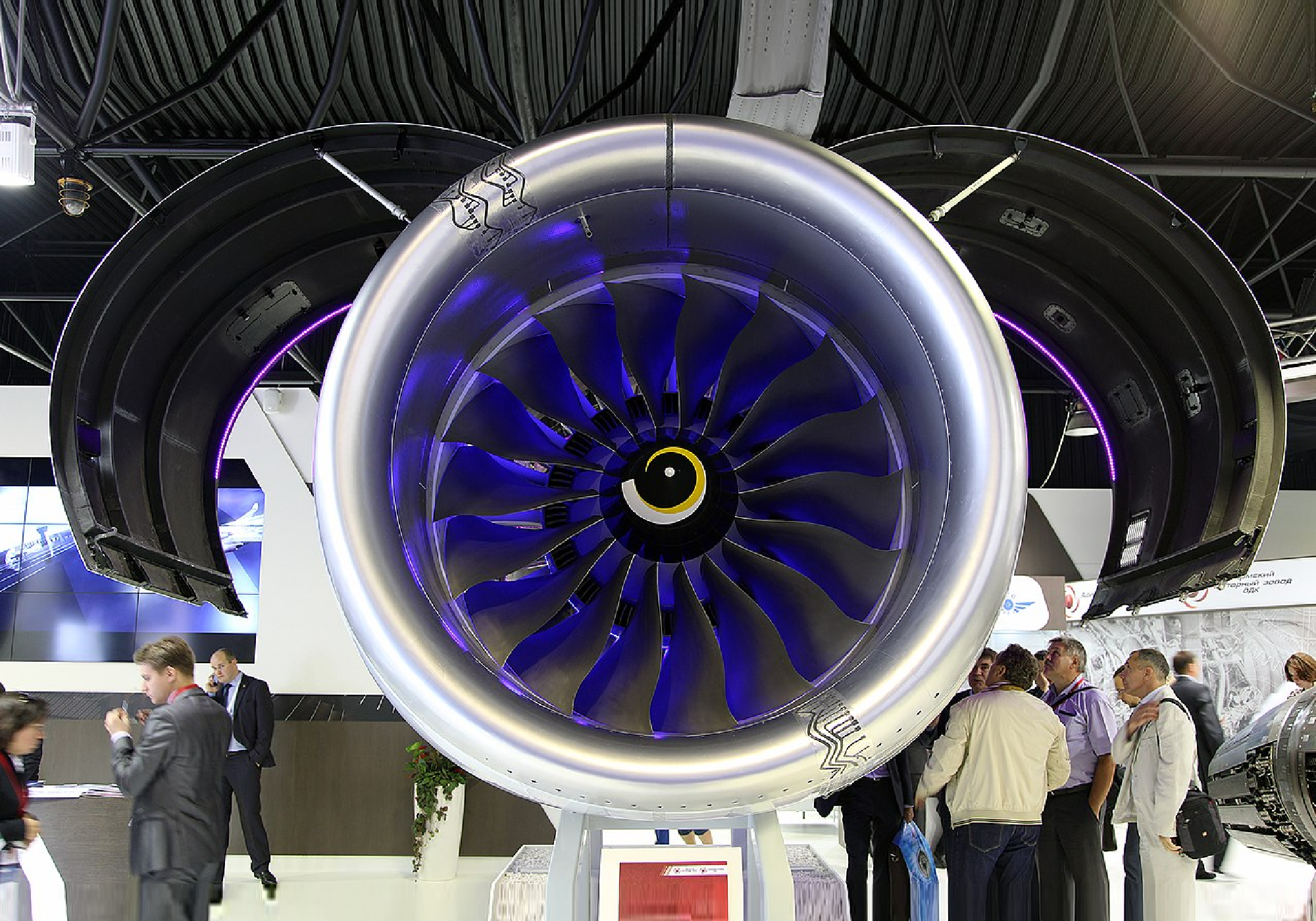
Engine nacelles consist of rigid panels interconnected by locks and form closed shells. Mounting the engine with a pylon is necessary to transfer all power factors to the aircraft structure.
In the design of the nacelles, there is necessarily a hood device – structural elements, engine hood flaps (Fig. 3).
- Firstly, they are necessary to protect the engine from atmospheric precipitation and mechanical damage.
- Secondly, providing convenient access to the engine and other units installed on it for their inspection, adjustment, repair and replacement.
⚡️ Metal/Polymer Composites
Airframe of modern aircraft for various purposes are mainly made of aluminum alloys (Fig. 4). The disadvantages of aluminum alloys, the most popular among which are alloys of the Al-Li, Al-Zn-Mg-Cu and Al-Mg-Si systems, include a small range and level of static strength, low resistance to fatigue crack growth and high density, which negatively affects the resource, survivability and weight efficiency of aircraft elements. Polymer composite materials, which have been intensively replacing aluminum alloys in recent years, increase strength and weight efficiency, but at the same time significantly worsen the fire resistance of aircraft elements.
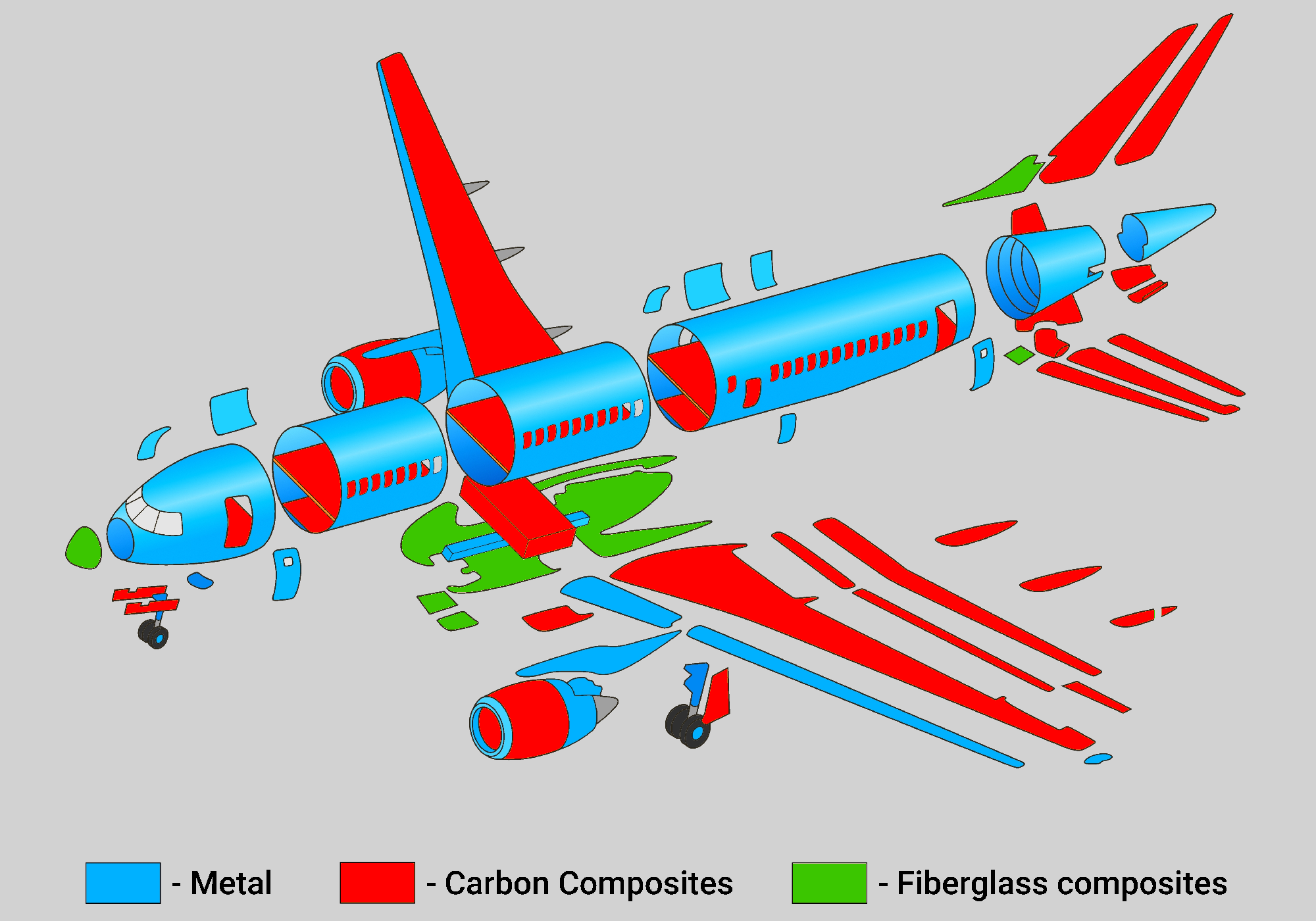
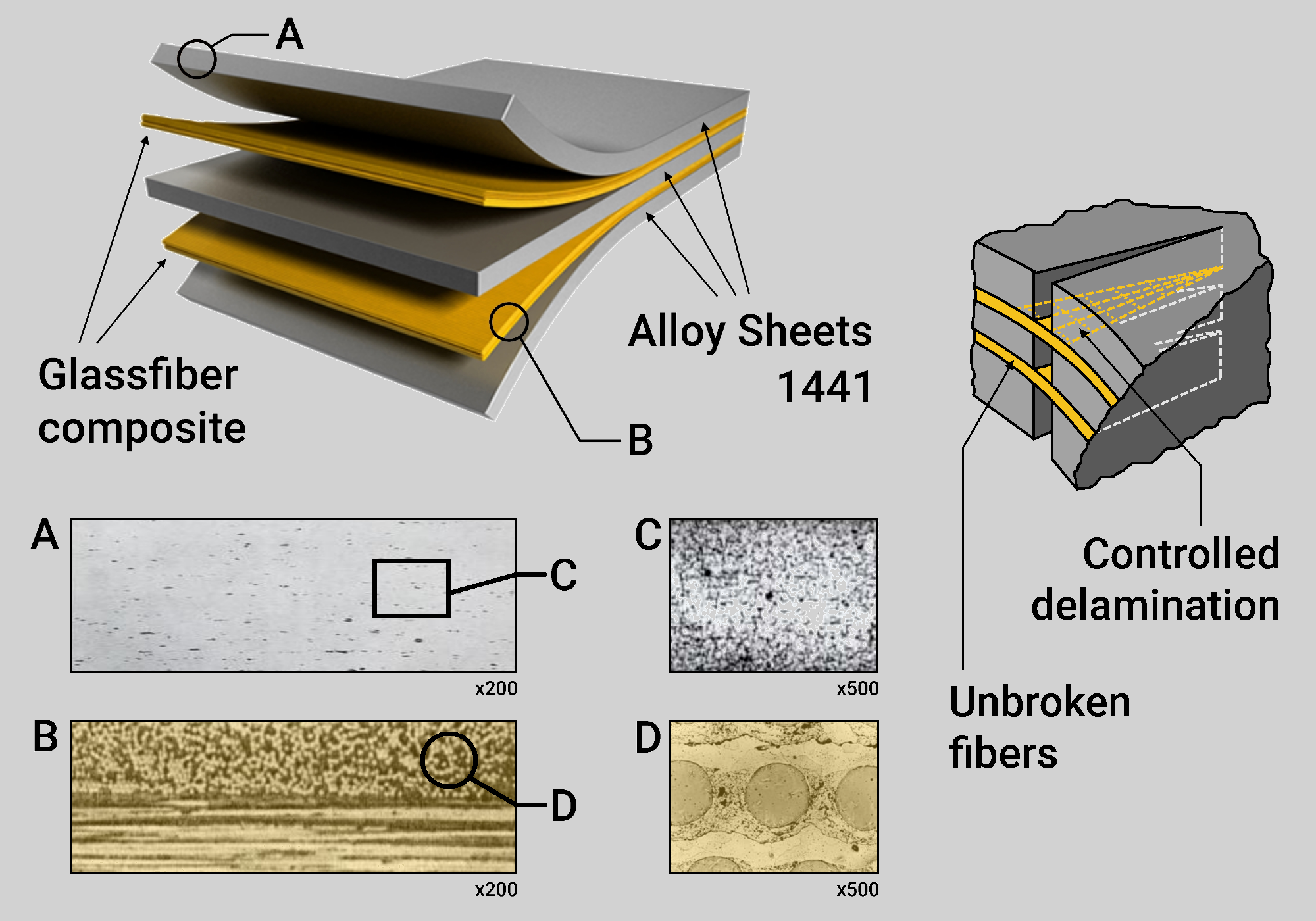
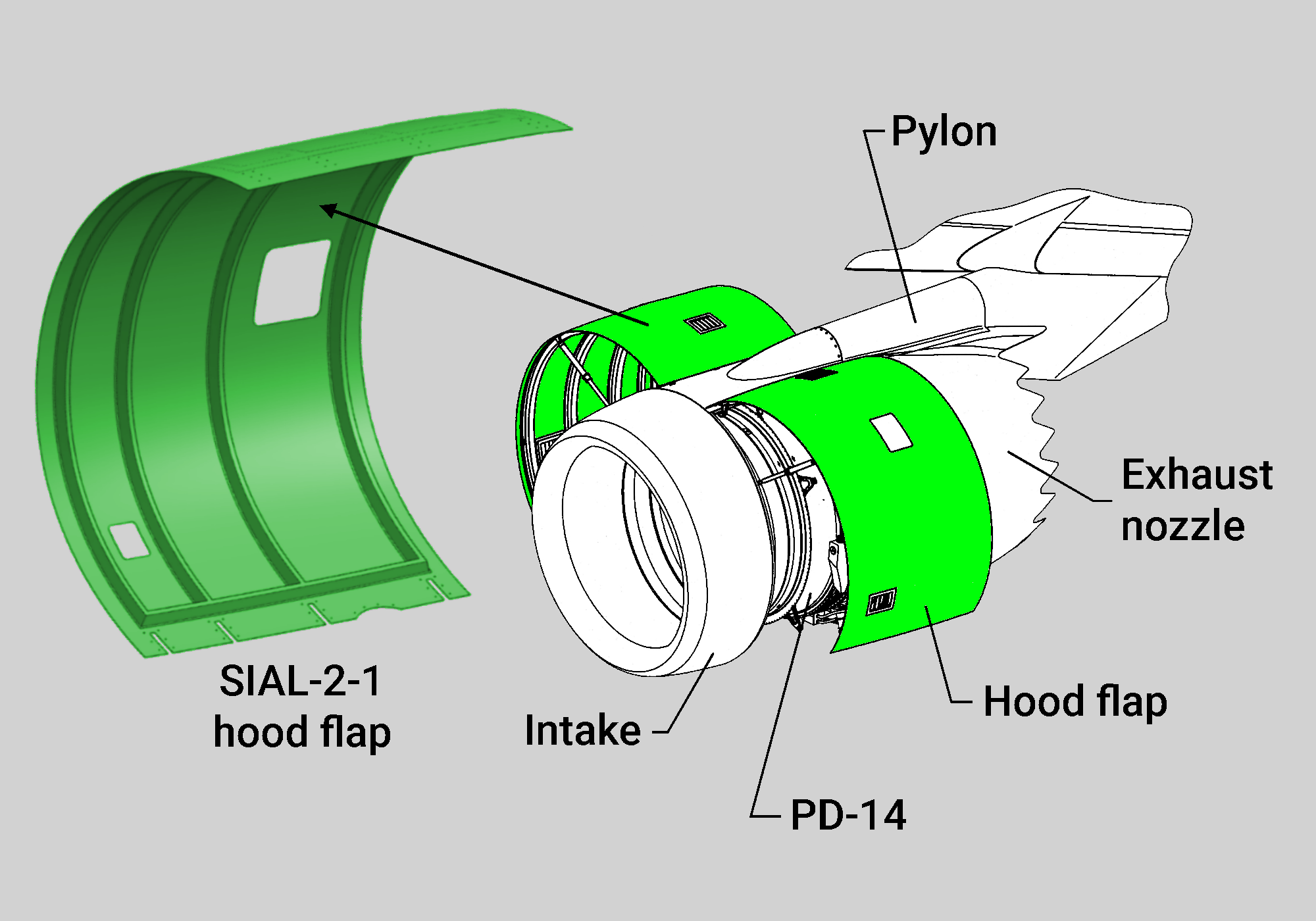
Aluminum−fiberglass materials, which represent a new promising class of hybrid sheet glued composite materials, are largely devoid of the above disadvantages. They are thin aluminum sheets with glass fiber interlayers of various reinforcement schemes, depending on the operating conditions of the aircraft element.
VIAM has developed a set of laminated aluminum-fiberglass plastics. Such as SIAL (Fig. 5). This layered hybrid material consists of thin (0.3–0.4 mm) sheets of Al–Li alloy of reduced density 1441 and interlayers of fiberglass. Layers of plastic consist, as a rule, of several monolayers of unidirectional adhesive prepreg reinforced with high-strength glass fillers; the location and number of sheets and layers are determined by the purpose and size of the part.
In this project, the task was to apply the SIAL-2-1 material in the hood flaps of PD-14 engines designed for Irkut MC-21 short- and medium-haul aircraft (Fig. 6).
⚡️ Results
As a result, important data on the strength characteristics of SIAL-2-1 (Zhivotenko, 2014), impact resistance and fire resistance were obtained (Fig. 7). A number of technological problems were discovered that prevented the immediate use of metal-polymer composites (Fig. 8).
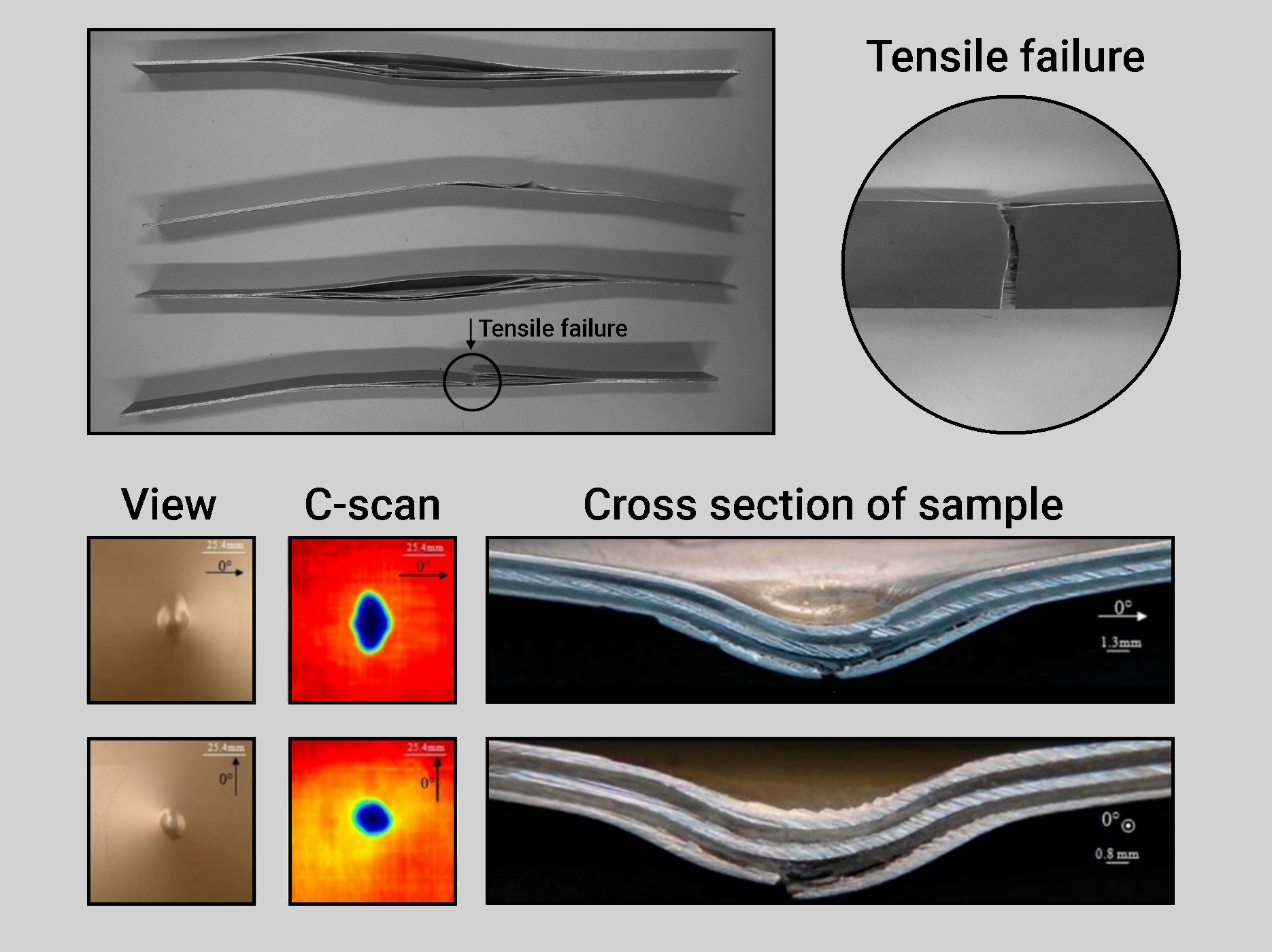
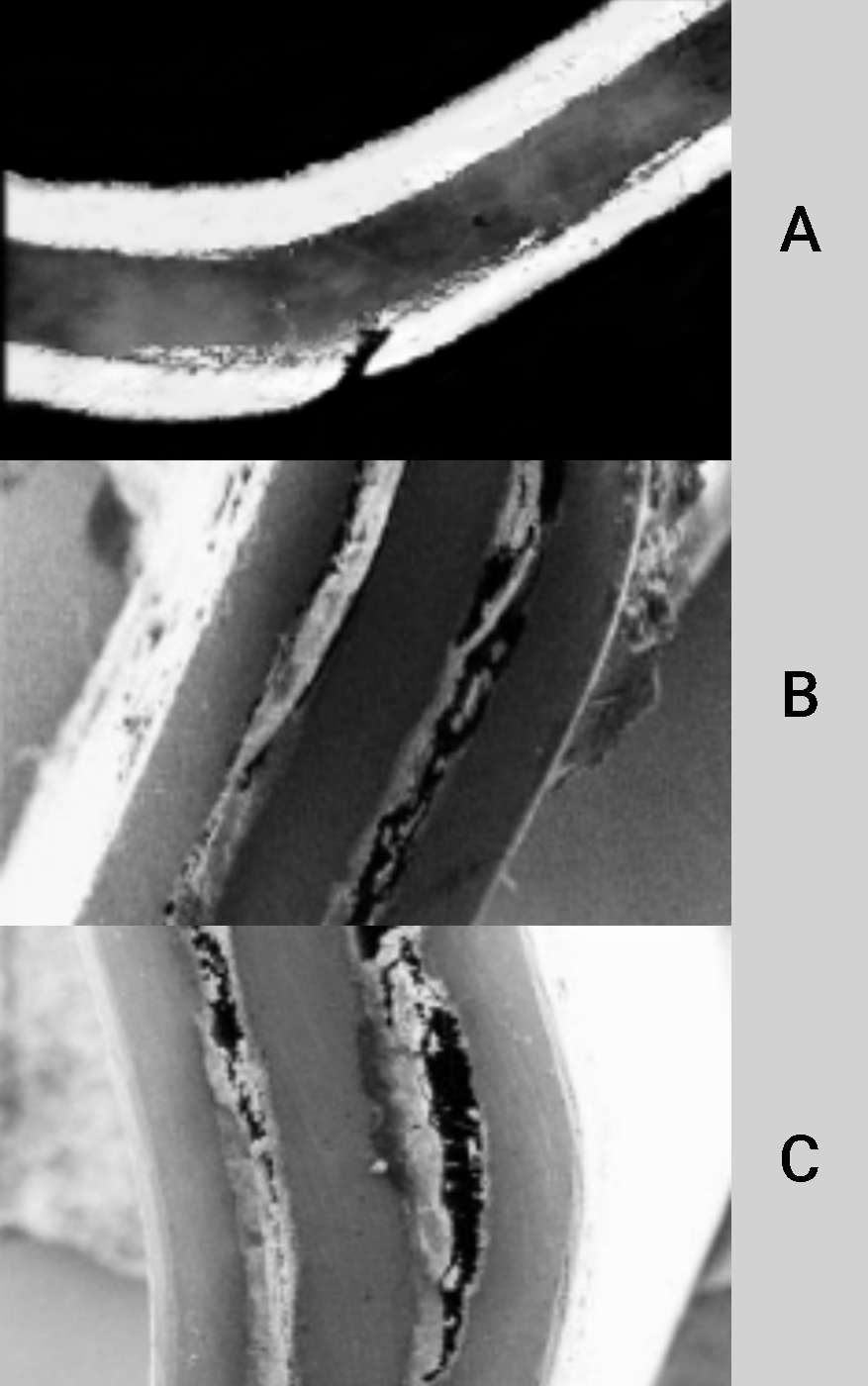